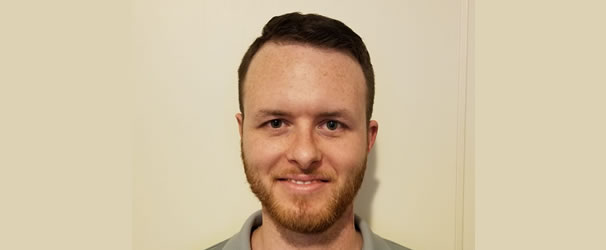
Guill provides helpful terms for extrusion
USA News
- July 2021
- Image: Denis Finn
Denis Finn, chief engineer at Guill Tool & Engineering, has compiled a glossary of useful terms used in the extrusion business. Mr Finn would welcome any feedback.
- Extrusion die assembly — also known as crosshead, inline tubing die, head, die. Connected to extruder by feed pipe/flange. Forms extrudate into desired shape.
- Tooling comprising two components — the tip and the die.
- Tip — defines ID of product for a tubing application or locates the substrate in a jacketing application. Tips are also known as pins or mandrels.
- Die — defines OD of product. AKA bushing.
- Land length — straight section at end of the tool set.
- Gum space — distance between end of tip and back of die land.
- Draw down ratio — relationship between ID and OD of tooling vs the ID and OD of the finished product.
- Linear draw — the ratio of the ID of the die and OD of the product; and the ratio between the OD of the tip vs the ID of the product.
- Area draw — the ratio between the cross sectional area of the output of the tooling and the cross sectional area of the finished product.
- Draw balance — ratio of the outer surface of the draw down cone to the inner surface of the draw down cone.
- Concentricity — how well centered the OD of the product is to the ID of the product or the jacketed substrate.
- Ovality — how round the OD of the product is.
- Dead spot — section of the flow where material is allowed to stagnate. Usually causes burning and degradation issues over time.
- Balanced flow — uniform exit velocity over the cross section of the product. A well-balanced flow produces a higher quality product.
- Fish eye, gel, unmelt, comet — common terms for unmelted or non-homogeneous melt.
- Melt fracture — surface defect in product caused by shear degradation (usually manifests as a grainy/frosted appearance on surface of extruded part).
- Die drool — particle build-up on outside surface of tooling. Build-up can break off and cause defects on finished product.
- Bulk residence time — amount of time polymer spends in the extrusion die assembly.
- Shear — term to describe a force that the melt experiences as it is forced through the extrusion die assembly.
- Viscous dissipation aka shear heat — frictional heat generated as a result of shear.
- Viscosity — resistance to flow.
- Cold spot — section of extrusion die assembly that is not adequately heated, resulting in imbalanced flow or a thermoplastic freeze off.
- Rheology — the science of characterizing a fluids behavior.
- Draw down cone — section of molten polymer as it draws down to its final product dimension.
- Calibrator — device to precisely establish and control the desired product dimensions.
- Stripe — feature to identify or establish orientation of finished product.
- Encapsulated — stripe between outside and inside surfaces of product.
- Embedded — surface stripe with established depth. Typically a percentage of the wall.
- Surface — stripe only on surface of product.
- Window — stripe that goes through wall from OD to ID.
- Surging — inconsistent melt output that results in product dimension variation.
- Coextrusion — any extrusion that uses two or more extruders.
- Wire line/pass line — distance between face of extruder to the center line of the crosshead.
- Direction of travel — a way to establish production line orientation.
- Recommended moisture content — a qualifier of how dry polymer should be before it is processed.
- Substrate — the material that is being coated in a jacketing process. Can be wire, bundle of strands, fibers, etc.
- Jacketing — covering a substrate with melt.
- Multi-lumen — a tube with multiple internal cavities.
- Melt probe — a device to directly measure pressure and/or temperature of the melt.
- Thermocouple — a device to measure temperature of the extrusion die assembly. Typically used to control heater output.
- Heater bands — provide heat to the extrusion die assembly.
- Flow distributor — shapes the melt to achieve balanced flow.