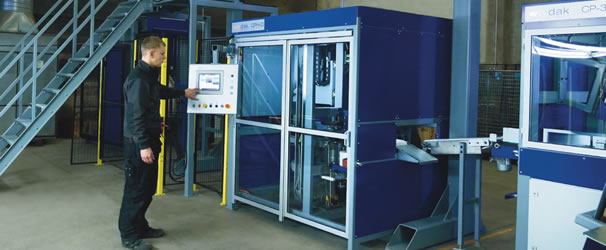
Advantages of automation in packaging equipment
Windak is promoting its automated cable packaging equipment as a means of providing increased productivity through automation, saving on cable packaging costs, optimizing labor utilization, reducing waste and maximizing output.
With customers increasingly demanding speed and quality, manual packaging can be a time-consuming process that can lead to delivery delays. Windak states that more than 40 per cent of the labor cost in cable factories is in the packaging area, so automation can lower overall operational costs.
Automation can also ensure quality and consistent accuracy while reducing mistakes, by eliminating the risks associated with manual intervention, as well as reducing production downtime.
Environmentally friendly packaging is Windak's top priority for the coming years. Its approach is to reduce the environmental impact on the whole production process. Sustainability continues to be an important factor for customers and their end consumers.
Windak is putting its emphasis on minimizing energy consumption by using the latest standards; lowering the volume of waste during the packaging process; and reducing space utilization.
The company's range of standard and customized equipment can be used for in-line operation with an extruder, or offline with a payoff, with options to cater to most packaging needs.
For example, Windak QuickPacs are high output coilers developed for the highspeed packaging of short length coils (up to 100m in length) of single conductors and/or flat cables. They are designed for both shrink film package and coil in a box.
The QuickPac series of coilers are capable of coiling 9-12 layer-wound coils per minute. Coil dimensions range from 120 to 400mm OD, and 100 to 180mm ID.