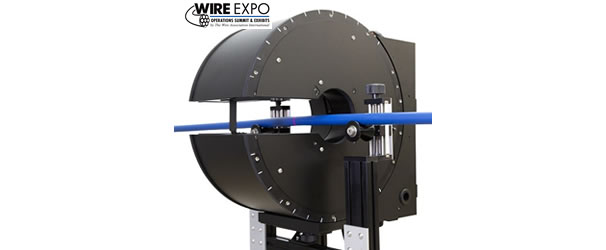
LaserLinc, Inc
Booth 819
LaserLinc, a specialist in open, scalable measurement and process control solutions, reports that there is surging demand to satisfy increasingly stringent quality standards. Manufacturers of high-value, high-specification cables are looking for easy-to-use solutions that reliably detect cracks, bumps, pits, wrinkles, scratches and similar defects, and also consistently and accurately measure diameter.
Unlike vision systems commonly deployed in the wire and cable industry, LaserLinc's FlawSense system uses laser-line triangulation technology to provide a 360° measurement of surface geometry, to detect defects regardless of product shape, orientation and colour, while being immune to ambient light variation. Defects are identified based on height, width and length variances that exceed user-specified thresholds derived directly from designed product specifications.
In contrast, vision inspection systems do not measure surface geometry and cannot identify defects based on actual dimensional characteristics. Without 360° dimensional data, vision systems are limited to identifying defects based on complicated artificial intelligence and pattern recognition algorithms or light intensity changes.
One of the main challenges with vision systems is dealing with false positives caused by factors such as colour variation, changes in ambient lighting and surface geometry. These systems also require significant training, making their deployment and use more complex.