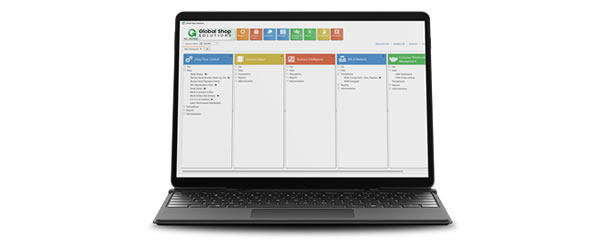
Transforming manufacturing with ERP software
Enterprise resource planning (ERP) software can be used to turn an inefficient manufacturing company into a lean business. ERP can provide a complete solution to efficiently run an entire organisation, touching on all critical aspects of the business, and allowing everything to be managed from a central location.
The systems can provide the data needed to make informed business decisions: people and processes become more efficient and productive; communication between departments improves; waste is reduced while sales, margins and quality increase.
Some of the main signs of an unhealthy
manufacturing business include:
- Untrustworthy data — paper documents and spreadsheets containing manual errors and inaccurate, outdated information.
- Hit or miss scheduling — using rough estimations to drive a manual scheduling process.
- Inaccurate job costing — lack of real-time data makes job costing historical rather than current.
- Incorrect work orders and routers — human error can cause shop floor mistakes that lead to missed due dates.
- Poor (manual) inventory management — parts and materials get misplaced, and purchasing buys too much or too little due to imprecise inventory data.
- Inefficient material movement — manual tracking of material with hand-written cards.
GSS states that with reliable ERP software, none of the above problems need to happen.
Generally speaking, companies that implement or convert to an ERP system will experience improvements such as:
- One "source of truth" — being able to trust all of the data collected, including production schedules and promised due dates. ERP enables this by tracking, organising and providing quick access to information.
- Fully integrated scheduling — instantly identify true labour and resource capacities, and carry out "what-if" scenario planning to see how potential schedule changes will affect other jobs.
- Precise job costing — providing detailed cost breakdowns for inventory, jobs sequences and cost of goods sold. ERP tracks every cost that goes into a project.
- Accurate work orders and routers — work orders act as the architectural blueprint for each job; routers provide the "road map" to get there. ERP electronically sends these critical documents to the shop floor.
- Digital inventory management — accurate inventory, with a few clicks of a mouse to show how much of a part or material is on hand, where it is, how much is already allocated to jobs, and when ordered parts will arrive.
- Mobile material movement — ERP transforms material movement by seamlessly aligning with mobile technology. Using handheld scanners and mobile devices, part movers can make material transactions from anywhere on the shop floor.