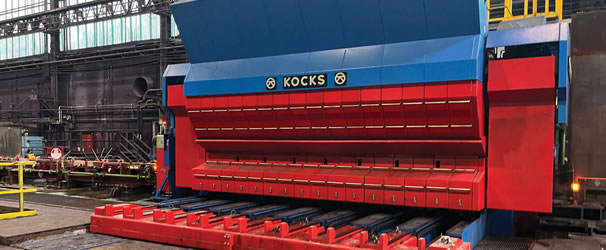
Successful integration of thee-roll intermediate block
Steel producer Nucor Steel Nebraska has rolled the first bar on its new Kocks intermediate reducing and sizing block.
The iRSB® is one of the latest advancements in Kocks's production technology and has been designed to increase flexibility in Nucor's rolling mill. Its design minimizes potential trouble spots and improves operator safety. Following the successful commissioning, the final acceptance certificate (FAC) was signed three weeks after the first bar was produced through the block.
Nucor Steel Nebraska is a division of Nucor Steel Corporation, the largest steel producer in the USA. The investment is part of a commercial strategy to align the product mix with current and future demand. The selection of the iRSB was based on the improvement of the whole rolling mill concept with regard to quality, flexibility, productivity and process safety.
With the Kocks three-roll intermediate block, more sophisticated material grades can be flexibly rolled, enhancing the steel producer's product portfolio without major changes to the overall layout of the rolling mill. The iRSB 370++/8 replaces eight traditional two-high stands, providing pre-sections in a tandem arrangement for the existing RSB® 370/5, which has been in operation since 2005.
Kocks also supplied the roll-shop equipment and its software solutions. The RSB is equipped with the Kocks 4D Eagle® profile measuring gauge, and is also connected to Kocks's Size Control System (SCS®), which allows real-time adjustment of the operating parameters of the rolling block. This enables transparent process monitoring and quick process adjustments.