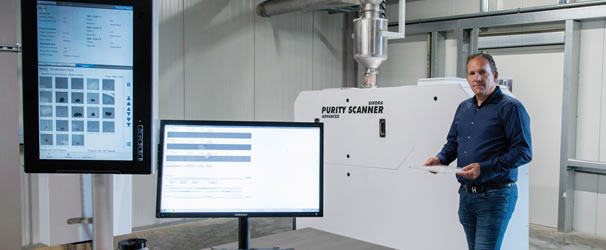
Inspection and sorting for material purity in contract sorting
Sortco GmbH & Co KG is a specialist in optical and mechanical sorting of shape and color deviations in plastic pellets. The company also offers dust removal and metal separation of plastic raw materials.
Since March 2021, Sortco has been using two Purity Scanner Advanced systems from Sikora in its new sorting service center in Niederzissen, Germany, to sort standard plastics as well as optically demanding technical plastics. With these systems, the pellets to be sorted are inspected 100 percent optically, and impurities from a size of 50µm are automatically sorted out.
Technically demanding plastics, such as those used in the medical sector or in the aircraft and automotive industries, require the highest quality standards as well as reliable control and processing of raw materials. The requirements for the purity of the materials are therefore also very high. Sortco has been specialized in contract sorting since 2015, and professionally prepares plastic pellets according to customer requirements.
Sortco uses the Purity Scanner Advanced to sort primarily transparent, natural-colored and colored pellets. The focus is on unreinforced materials for use in high-quality optical applications. Each system is equipped with three optical cameras, which detect optical impurities and sort them out using compressed air. The Purity Scanner Advanced can also be extended by an X-ray camera for the detection of metal particles in the raw material.
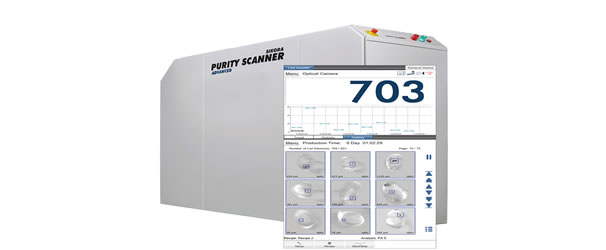
Black specks are the focus of our sorting work. In addition, we remove all discolorations that have a different color than the polymer to be sorted,
said Hilger Groß, head of sales and QM at Sortco. As a service provider, Sortco is confronted with new materials and new and old contamination every day. This means that we also have to adjust the Purity Scanner Advanced to constantly changing products and customer requirements. We therefore create a special recipe for each product that can also be used and adapted for future jobs.
During sorting, the Purity Scanner Advanced automatically records the number of defects, the smallest edge length of the optical defect, the contamination area and, for example, the size class of the defect, which can be freely adjusted and specified according to customer requirements. In addition, the system detects the intensity with which the color deviation was detected.
All key data is checked again at the end of the job, stored, and a test report is generated for the customer. Logging of the results is also possible.
Sortco managing director Lars Ruttmann expects increasing demand for optically sorted raw materials in the future: Sorting is in demand because manufacturers have recognized that special requirements also necessitate special measures. We are pleased to have found such a reliable partner in Sikora and its sorting system, with whom we successfully cooperate in our core business.